The picture at left shows my shop set up which consists of our garage, four sawhorses and an old picnic table, which I can convert into a twelve foot long workbench with the addition of two pieces of particle board when needed. Due to my permanent workbench and wall storage in the rear of the garage, my assembled boat hull just fits with a couple of feet of work space at the bow and stern. I'm using almost the entire available floor area for the project. I've read that some people have assembled Skerrys and kayak kits in basements and apartments. I'm sure this can be done, but I'm glad I have this venue and could even use a little more space than I have.
I started out the week with final sanding of the hull. I had previously filled in the all the stitch holes with wood fiber thickened epoxy, which leaves brown marks around each hole. Since I'd already decided to paint the hull I wasn't too concerned with eliminating all remnants of these marks by a thorough sanding. I was also a little gun shy after sanding through the veneer around the puzzle joints in a couple of places. It's not real clear in the instruction book whether brown marks as opposed to blobs of thickened epoxy would disappear after applying the subsequent coats of clear epoxy, so I was curious what would happen. Well, they don't disappear. That's a lesson I'll remember when finishing the interior which I plan to leave "bright" or natural, with just a coat of varnish over the clear epoxy.
After sanding I cleaned the hull by first vacuuming and then wiping down with denatured alcohol. The bottom panel and adjacent garboards were to be covered with fiberglass cloth, a process that I dreaded a little due to an unfortunate past experience. All went well, though, and I was able to smooth and stretch the cloth with clear epoxy applied with a vinyl squeegee and it conformed perfectly to the bottom. This slow curing epoxy is really easy to work with in these situations, giving you plenty of time to fix little imperfections.
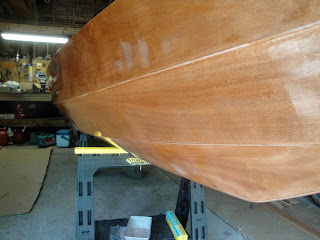
Two more coats of clear epoxy over the entire hull, applied with a roller and then tipped out with a foam brush, separated by at least five or six hours of curing time and I was done. It turned out pretty nice.
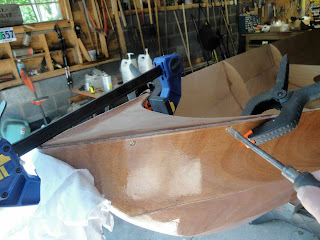
Next was the installation of the breast hooks. There was some rasping and sanding involved to make sure the pieces conformed to the shape of the sheers, fore and aft. The Shinto saw rasp is really coming in handy for these types of tasks. The hooks were then glued and screwed into place.
Since I would have to return to Minneapolis for a few days I decided to get some of the time consuming gluing out of the way. The first was the rails which are four in number and come in three pieces each, with the scarfs mercifully pre-cut. As these will be under a lot of stress when fastened to the sheer the manual recommends letting the epoxy cure for a minimum of 48 hours. I'm starting to use the mass quantities of spring clamps and C-clamps I've purchased.
I skipped ahead in the manual and found that I needed to glue together two identical skeg (goes on the bottom of the hull) pieces at some point, so I decided to do that now. I could now leave my north woods workshop secure in the knowledge that for a time at least my project was taking care of itself.
When I return I've some planing of the assembled rail pieces to do. Then I'll start to install the gunnel rails (inwales and outwales in boat jargon), another adventure for sure.